
Modular Surgical Glove.
DePuy Synthes
Medical Device Design
This project was drafted by DePuy Synthes, an expert in joint replacement, medical tooling and part of the Johnson & Johnson Medical Devices group. DePuy required a modular, cut-proof surgical glove to provide medical staff with greater functionality in the operating theatre. Our team offered a creative perspective to discover what is possible within the scope of a glove. The standard surgical glove has to adhere to numerous strict specifications. Primarily, and most importantly, it forms a sterile barrier between the surgeon and the patient. It must be chemically inert and easy to don, preserving both hand locomotion and finger dexterity. The project’s main objectives were to determine what additional functions could be feasible whilst providing a cut-proof barrier.
Skill development: Design Process, Arduino Programming, Electronics, Material Science, Rapid Prototyping, Testing, Big Data, Client Relationships, Report Writing, Leadership, Teamworking, Presentation

A solution for a future in Big data.
Whilst in the operating theatre, surgeons use tools and sensors to read patient vitals. This project explored the concept of using the glove as a base for sensors and tools, functioning in two principal modes.
Proactive.
Removable sensors and tools attach to the fingers, giving the surgeon real-time data displayed on a screen on the forearm. These include Ultrasound sensors, IR sensors, torchlight and cameras.
Reactive.
Locomotion sensors embedded in the glove record hand motion for archiving and training purposes to be analysed post-surgery.
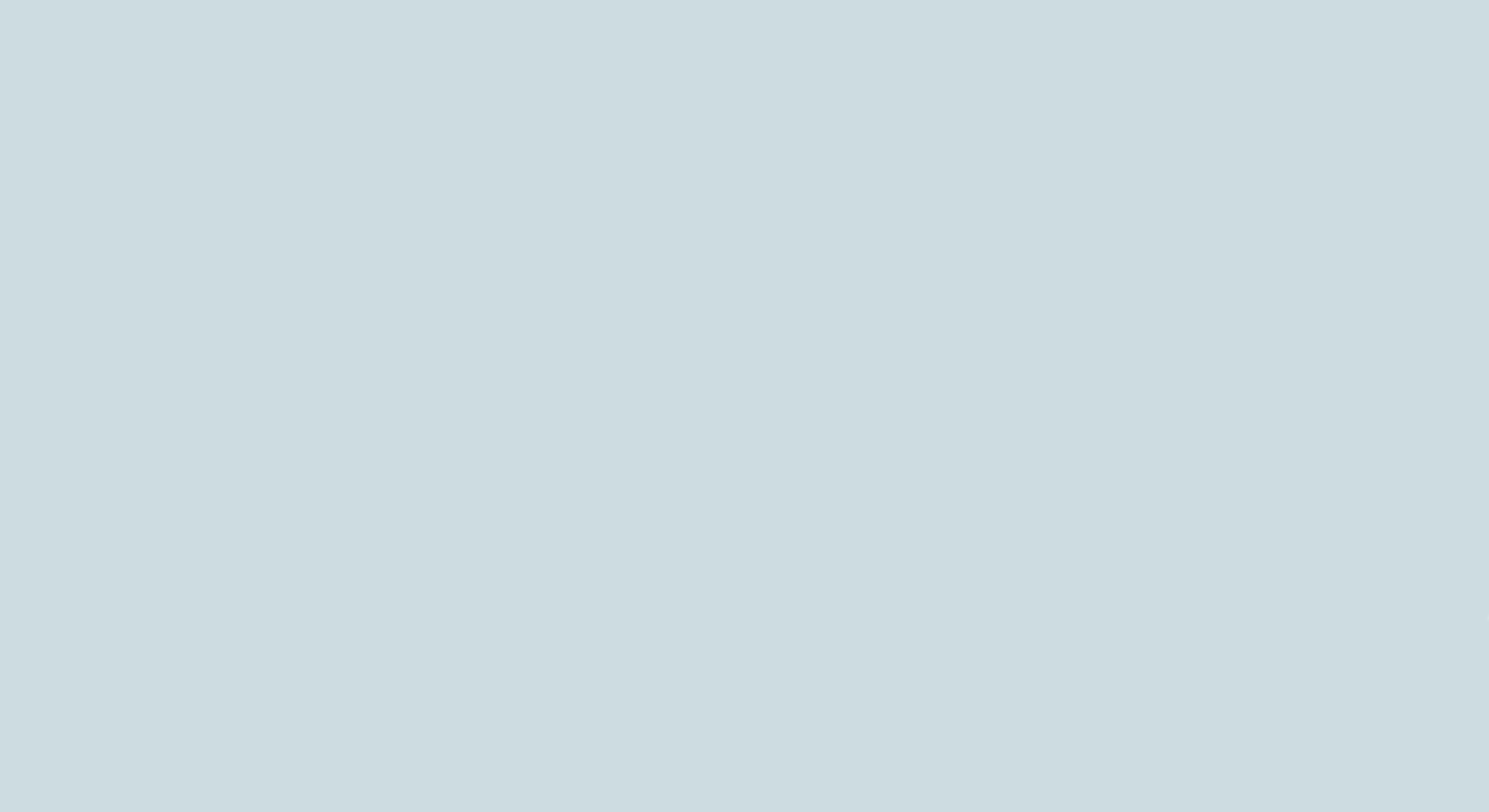
Materials turn abstract,
into tangeble.
Technical knowledge of material science and mechatronics was essential to realise the scope of the project. Specifications told us the glove needed to be cut-proof, sterilisable, maintain hand locomotion and finger dexterity.
Dyneema® was chosen as a suitable material for the base layer, providing cut-proofing whilst maintaining finger dexterity. A flexible TPU auxetic pattern membrane then acted as unobtrusive scaffolding to attach sensors and house electronics. The auxetic quality of the membrane ensured the surgeon could use a full range of motion. Electronics such as strain sensors, power and data links were to be embedded in the membrane so the glove could be sterilised and reused.
Knowledge of electronics and programming was necessary to embed wiring and strain sensors which link to the Wearable Processing Unit (WPU). The WPU is the brain of the glove, providing the sensors with power, data storage and displaying information for the surgeon.
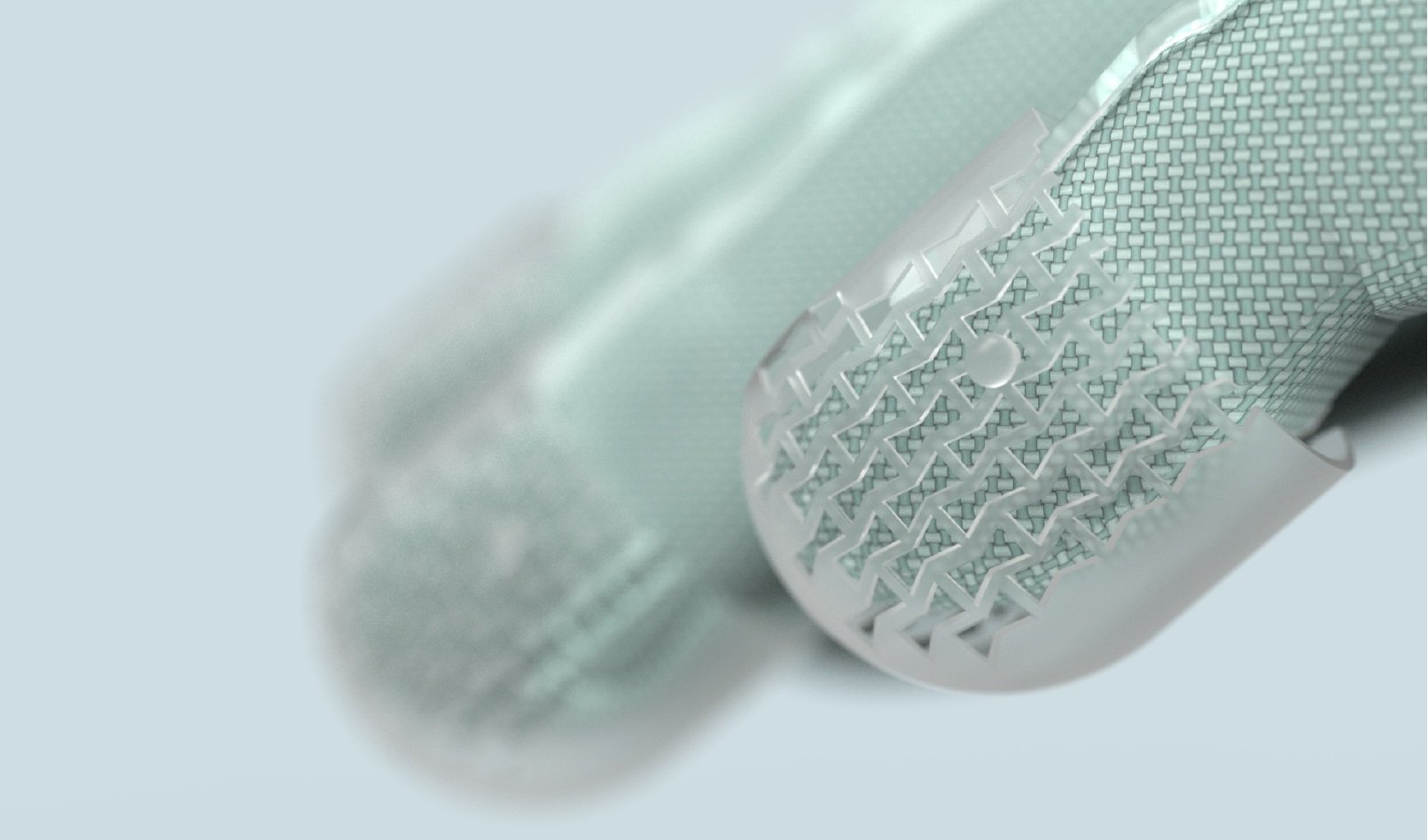
Collaborate towards
product success.
Collaboration was fundamental in ensuring we understood our users. Close contact with medical professionals provided the team with a window into the medical environment, offering insight into use cases and product use cycles. The team worked closely with Depuy in regular meetings to pitch ideas and assist in development. This required the team to convey ideas concisely and professionally through reports and presentation material.
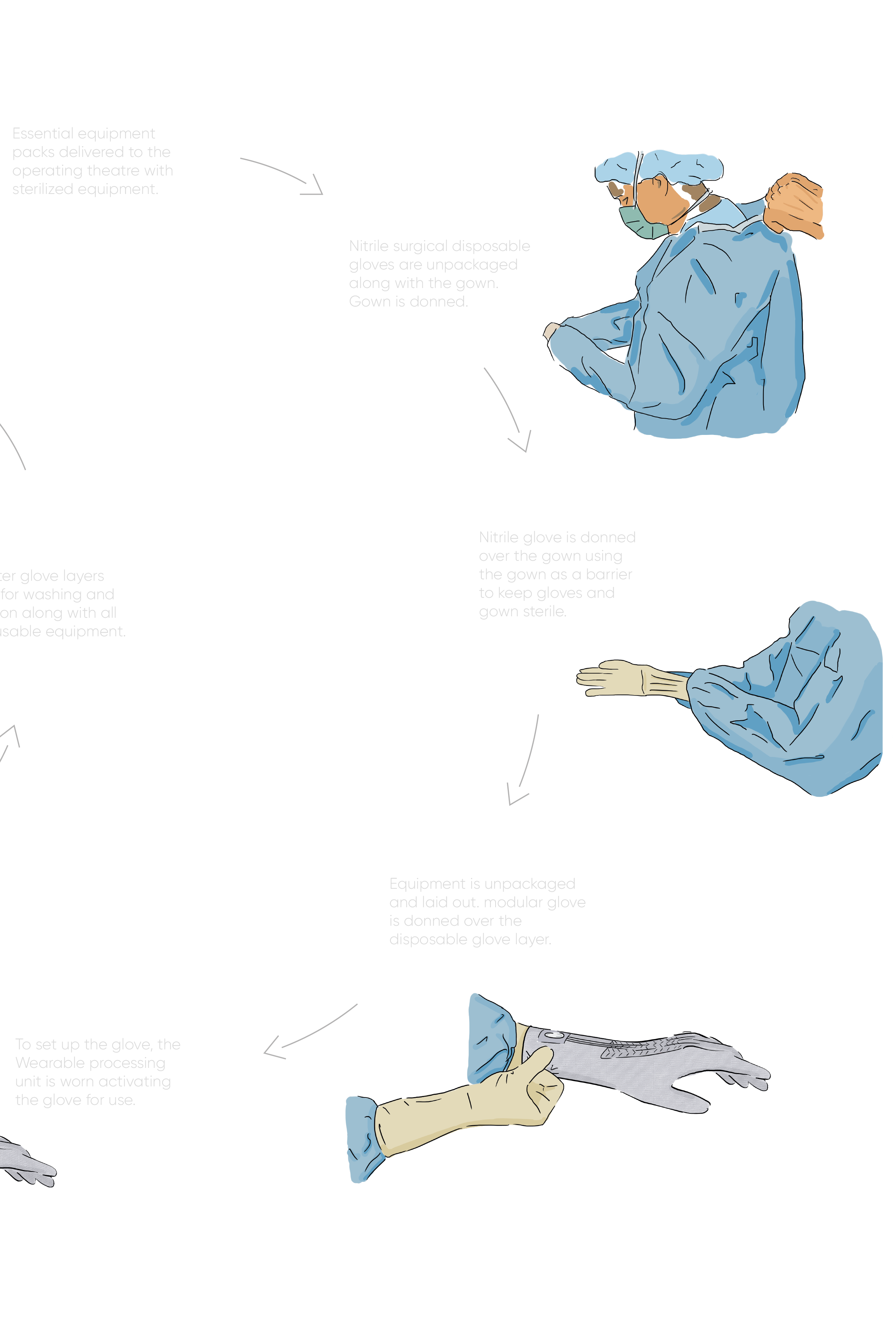
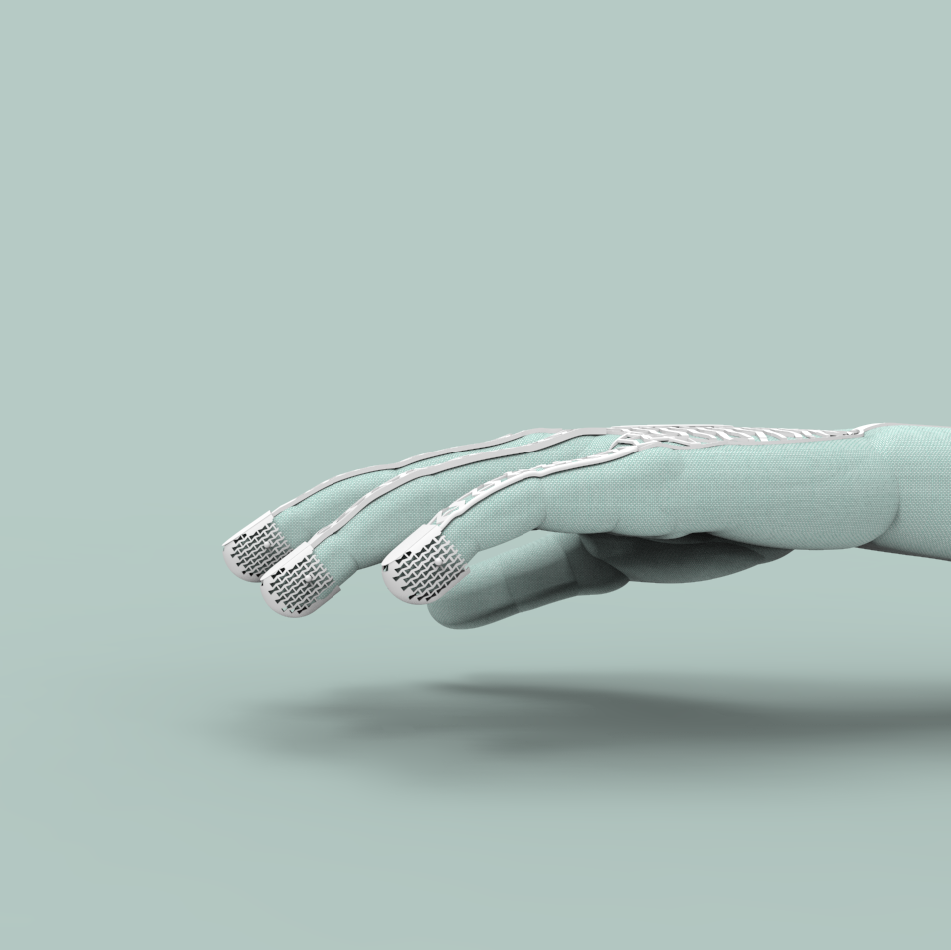